At first glance, the tariffs encouraged many U.S.-based companies to diversify away from China, a long-dominant supplier. Nearshoring gained traction, with operations moving to Mexico and Southeast Asia to reduce exposure to rising costs and political risks. This shift promised supply chain resilience, shorter lead times, and better risk mitigation. However, the transition wasn’t without growing pains.
Relocating supply chains is a complex, time-consuming process. Many businesses lacked the infrastructure, supplier relationships, or visibility needed to adapt quickly. The result? Delays, increased operational costs, and a scramble for qualified local partners. For smaller firms in particular, the financial burden of shifting production became a major challenge.
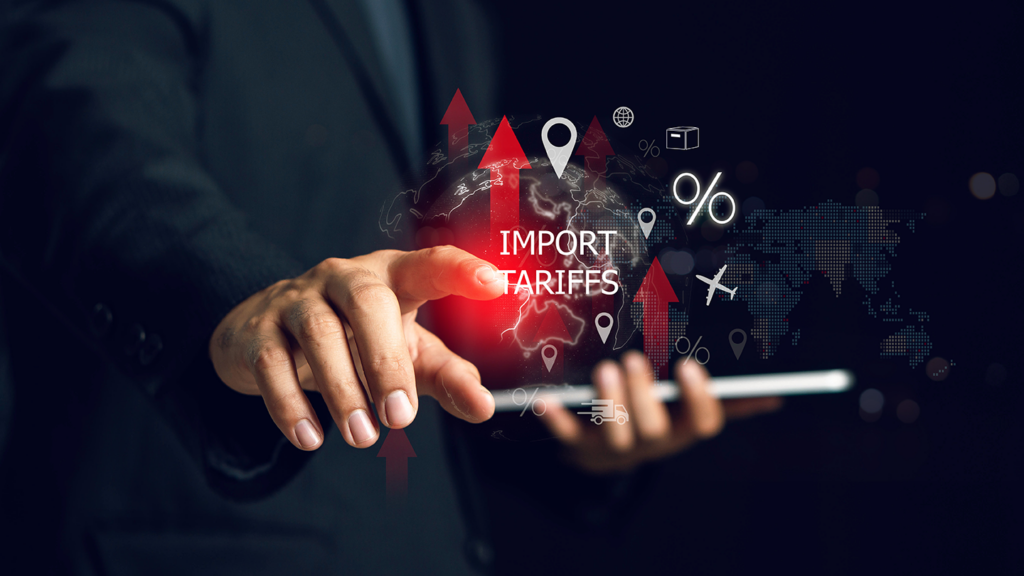
The tariffs also created uncertainty, complicating customs procedures and increasing compliance costs. Many companies, unsure of future policy changes, hesitated to invest in new logistics systems or long-term supplier contracts. This hesitation created inefficiencies and bottlenecks, particularly at U.S. ports and distribution centers already struggling with labor shortages and capacity limits.
From a resilience standpoint, the jury is still out. While some companies have successfully adapted by integrating new technologies and diversifying their supplier base, others remain in limbo—paying more for goods, struggling to meet demand, and facing unpredictable delivery schedules. In many cases, tariffs have exposed weaknesses rather than built strength.Conclusion
and boost your Supply Chain Management